Rotomolding Processing
After an item comes out of the Mold and is allowed to cool the processing of the part or item begins. Depending on the type of item , there are different levels of processing. If it’s one of our Water Tanks for example , processing will involve visually inspecting the tank for any defects inside or out. Bulk head fittings will need to be installed and the man hole cover fitted and attached.
Some of our more complex products like our Titan series hand wash stations will require more time for processing. These are multi piece items that will need assembly , inspection and testing to insure they go out the door as a complete functioning unit.
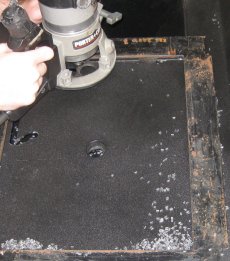
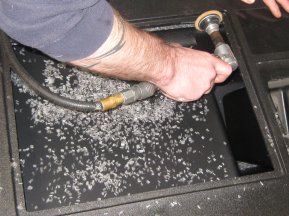
Since we do quite a bit of custom work for our customers, we have experience in all types of processing work. Some of which involves clamping a part or product as they come out of the mold, to a frame that holds it in place as it is allowed to cool. This insures that when the part cools it retains the shape needed to meet the required specifications of that product.
After the part cools, the clamps are removed and the part is taken to its next step in the processing process. Here the item is fitted with a custom made trim fitter or Jig for the jigging process.
The trim fitters allows for precision cutting and routing of the part so that the specifications are met each and every time whether the order is for 10 pieces or 100 , so no mistakes are made. This saves valuable time and allows us to produce a quality product on each and every run we do of a given item.
So the processing phase really involves the final work done after a product has been molded and after it has cooled sufficiently to work with, and is where the quality control really begins and ends.
After the processing is finished the product is then ready to be boxed or palletized and readied for shipment to the customer.
